Devashish’s HNBR Rubber compounds are what you seek!
HNBR represents a range of synthetic polymers known for their physical strength and resistance to heat, Oil & Chemicals. Hydrogenated nitrile polymers are manufactured by the catalytic hydrogenation of conventional nitrile butadiene rubber (NBR) polymers.
The nitrile groups are unaffected during the process, but the carbon-carbon double bonds in nitrile rubber are converted into more stable single bonds. As a result, we can manufacture and supply different grades through precise control of the proportion of unconverted double bonds in the material - 10% is considered an upper limit, but grades containing 4-8% (partially hydrogenated) or virtually no double bonds (fully hydrogenated) are used in most cases.
Choose your HNBR Compound properties
When selecting an HNBR polymer for a specific application, there are three criteria to consider:
Acrylonitrile content
Fluid resistance and low-temperature properties.
Hydrogenation level
Influences heat, chemical and ozone resistance.
Polymer Mooney Viscosity
Affects the compound's processing and the final article's physical properties.
Effect of Saturation
HNBR Compounds are highly saturated nitrile polymers consisting of acrylonitrile groups, ethylene chains and butadiene carbon-to-carbon double bonds. After hydrogenation consisting of acrylonitrile groups, this structure provides oil, fuel and solvent resistance, good abrasion resistance, and high physical properties. The saturated ethylene chains provide rubber elasticity, chemical stability, heat resistance, and ozone protection. Hydrogenation increases with the base nitrile polymer, and elongation property changes with increasing saturation and improves in direct relation to saturation. The presence of a small amount of the unsaturated butadiene group, typically between 0.2% and 15%, allows vulcanisation with sulfur or peroxide cure systems.
Effects of ACN Content
- The ACN content is one of two primary criteria defining each specific HNBR grade. In addition, the ACN level, because of polarity, determines several basic properties, such as oil and solvent resistance, low-temperature flexibility/glass transition temperature, and abrasion resistance.
- Higher ACN content improves solvent, oil, abrasion resistance, and glass transition temperature.
- The increase in ACN content Processability delivers Cure Rate with Sulfur Cure System, Fuel Resistance, Oil Resistance Compatibility with Polar Polymers, Gas Impermeability, Air Impermeability, Tensile Strength, Abrasion Resistance, and improved Heat-Aging.
- Today, HNBR ranges from approximately 17 to 50 %. Therefore, it affects not only the fluid content but also low-temperature performance.
- Higher ACN content means poor low-temperature flexibility.
Effect of RDB Content
- An HNBR with different amounts of RDB (residual double bond) contents can be produced by controlled hydrogenation of NBR.
- HNBR with high RDB can be cross-linked using Sulfur and Peroxide.
- High RDB increases crosslinking density.
- High RDB increases the compression set and reduces the ageing stability of the material.
HNBR Compounds range includes materials that cater to your requirements
Automotive
With the trend of ever-decreasing space in the engine bay, temperatures continue to rise, placing ever more demanding requirements on the components operating in this environment. One consequence is the need for Elastomers capable of ever-greater long-term high-temperature resistance and the capability to withstand harsh environments in the engine compartment. In addition, higher operating temperatures have resulted in the development of more aggressive automotive fluids and lubricants, further necessitating speciality elastomers combining more significant heat and fluid resistance. The automotive industry seeks a tough elastomer with improved chemical, fuel, and heat resistance.
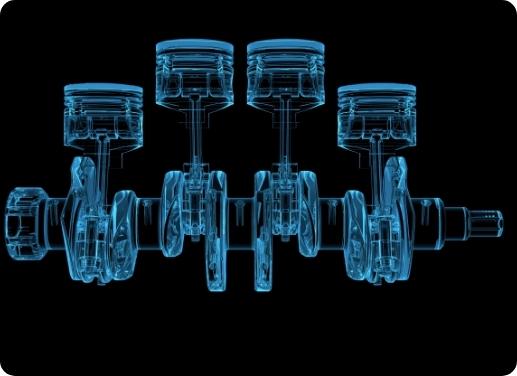
Oil Industry
HNBR compounds meet the extreme demands in oilfield applications such as resistance to corrosion inhibitors, Hydrogen sulfide / Sour gas, resistance to crude and drilling fluids, High Tear and Abrasion resistance, and Low water swell. In addition, low compression set and, most importantly, excellent resistance to Extrusions and Explosive Decompression (Rapid Gas Decompression) are seen in today’s oilfield industry. While HNBR polymer can withstand the harsh abuse encountered in drilling operations, these compounds can also withstand the high temperatures and pressures experienced in the well.
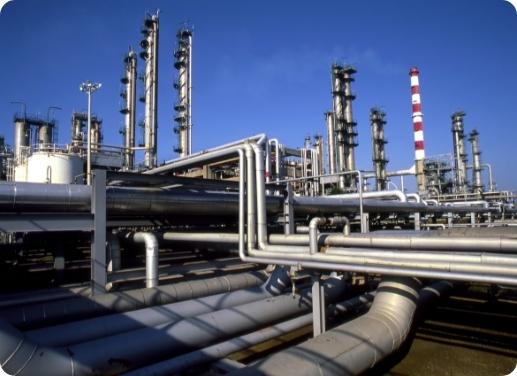
Industrial and Other Applications
Due to the ethylene content of HNBR polymers, they are resistant to many chemicals used in the roll industry, offering excellent heat and steam resistance; for plate heat exchangers for Fat/Oil applications. It provides high-temperature resistance and low compression set at high temperatures, including FDA. It is also used as an expansion joint, Industrial pump, Coupling etc., for excellent dynamic properties and heat resistance.
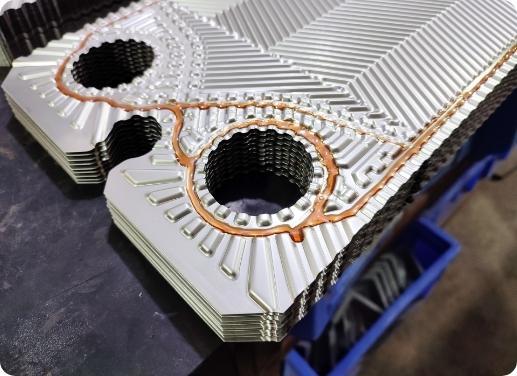